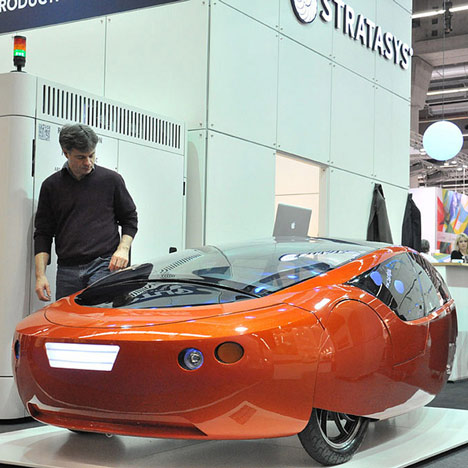
News: a fuel-efficient
3D-printed car is set to hit the road in two years, according to its US-based
manufacturer RedEye On Demand.
The three-wheeled, two-passenger vehicle comprises 40
large 3D-printed thermoplastic parts, compared to the hundreds of parts found
in a normal car.
The URBEE 2 is being
developed by RedEye On Demand and
its parent company, 3D printer maker Stratasys, in
collaboration with KOR EcoLogic.
So far in its development, 3D printing has largely
been used to produce unique or customisable items in single editions or small
runs, but the arrival of the URBEE 2 suggests it could also be applied to mass
production on a huge scale.
"A future where 3D printers build cars may not be
far off after all," said Jim Bartel, vice president of RedEye On Demand.
"URBEE 2 shows the manufacturing world that anything really is possible.
There are few design challenges additive manufacturing capabilities can’t
solve."
Once it's road-ready, the designers plan to drive
URBEE 2 from San Francisco to New York on just 45 litres (10 gallons) of
biofuel such as ethanol.
The car is a follow-up to KOR EcoLogic's 3D-printed
URBEE prototype, which was launched in 2010.
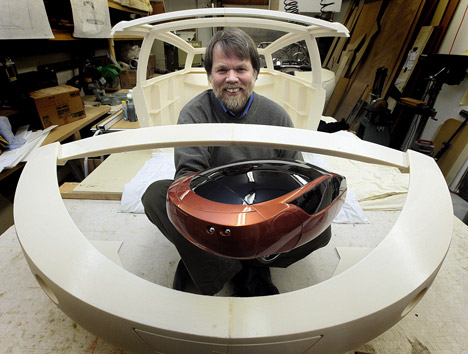
We've been closely following the rise of 3D printing,
reporting on plans to 3D-print a plastic house and a pen that sketches out 3D shapes in mid-air –
see all 3D printing news.
Other cars we've published lately include a car with light-up wings by fashion designer Jeremy
Scott and Audi's shape-shifting OLED headlights –
see all
car design.
Here's the press releases from RedEye On Demand:
At RedEye On Demand, 3D Printed Cars Edge Closer to
Production
Road-ready URBEE 2 will set new precedent for building
fuel-efficient vehicles
Minneapolis, March 7, 2013 – RedEye On Demand, a rapid
prototyping and direct digital manufacturing service, and its parent company
Stratasys, Ltd. (NASDAQ: SSYS) today announce a collaboration with KOR EcoLogic
to produce URBEE 2, the first road-ready, fuel-efficient car built using 3D
printing, or additive manufacturing, technologies. Targeted to hit the road in
two years, URBEE 2 represents a significant milestone in the world of traditional
assembly-line manufacturing.
"A future where 3D printers build cars may not be
far off after all," said Jim Bartel, Stratasys vice president of RedEye On
Demand. "Jim Kor and his team at KOR EcoLogic had a vision for a more
fuel-efficient car that would change how the world approaches manufacturing and
today we’re achieving it. URBEE 2 shows the manufacturing world that
anythingreally is possible. There are few design challenges additive
manufacturing capabilities can’t solve."
The KOR EcoLogic team will fully design URBEE 2 in CAD
files, sending them to RedEye On Demand for building through Stratasys’ Fused
Deposition Modeling (FDM) process. This unique process applies thermoplastics
in layers from the bottom up, yielding parts that are durable, precise and
repeatable. The finished two-passenger vehicle will comprise 40 large,
intricate 3D-printed parts compared to hundreds of parts in the average car.
The strong, lightweight vehicle will be designed to go 70 mph on the freeway,
using a biofuel like 100 percent ethanol. The goal is for URBEE 2 to drive from
San Francisco to New York City on only 10 gallons of fuel, setting a new world
record.
“As a mechanical engineer, I’ve always believed we
could use technology to help us solve some of society’s greatest challenges,
like minimizing our dependence on oil and reducing ozone emissions. How cool is
it that American manufacturing can evolve to tackle these challenges head-on?
Our team is excited to launch URBEE 2, putting a next-generation vehicle on the
road that will eventually be sold to the public,” said Jim Kor, president and
senior designer for Winnipeg-based KOR EcoLogic.
URBEE 2, which stands for urban electric, follows in
the tracks of its conceptual predecessor, Urbee 1. Produced in 2011 as a
partnership between KOR EcoLogic, Stratasys and RedEye On Demand, Urbee 1
proved that 3D printing could in fact produce large, strong parts that meet
accurate specifications of a car body. URBEE 2 will take the basic concepts of
Urbee 1 to a higher level, including features like a fully functioning heater,
windshield wipers and mirrors.
“With the Urbee 1 project, I learned that product
design is nearly unencumbered by considerations on how parts can be made with
digital manufacturing. That liberation is incredibly powerful and holds a lot
of potential for the future of manufacturing,” said Kor.